Hi All,
my BL-65 was converted to a Continental back in '65-'65. I've got cowl bumps and cracks in the panels. I've been working hard to rebuild the bottom cowl section and am pretty happy with the results:

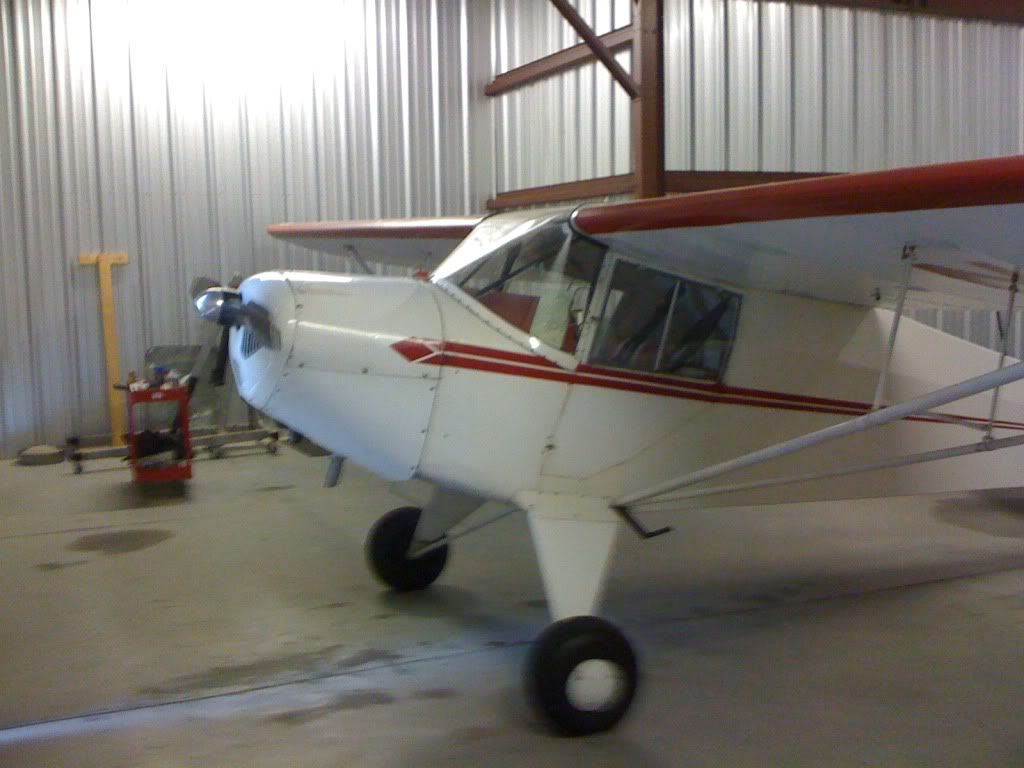
So now I need to tackle the top cowl sections. I'd love to get rid of the cowl bumps, but I have NO clearance on the top. Looking at the nose bowl from the front, I have very little gap at the top and lots at the bottom of the prop hub hole.
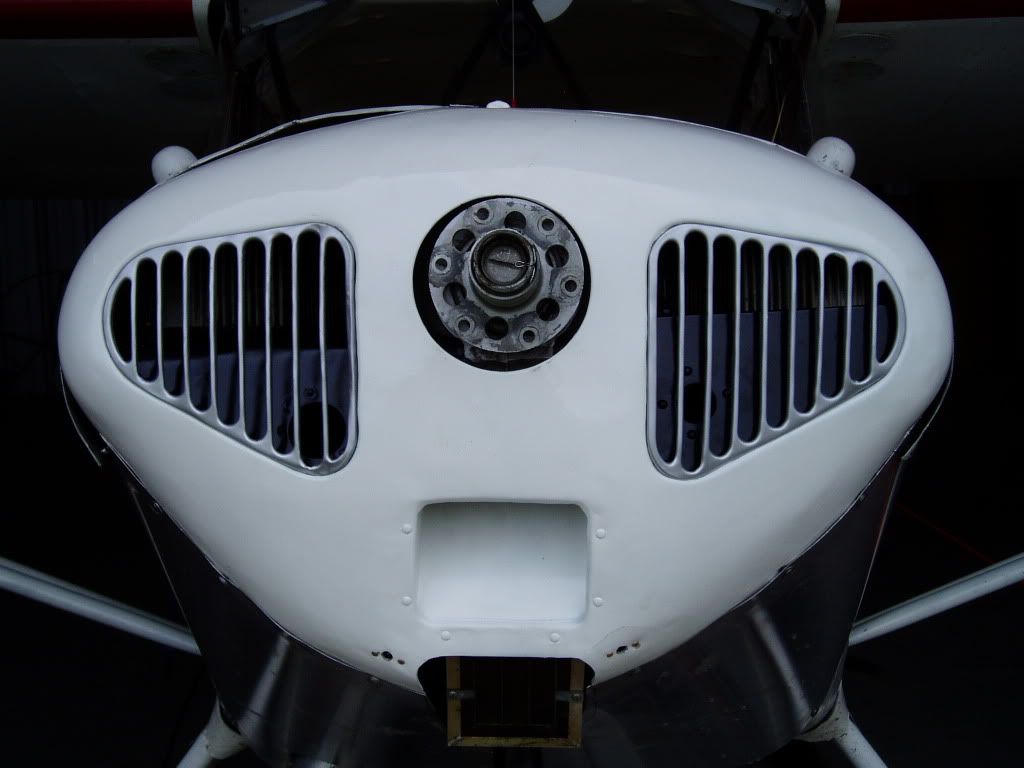
It was like this when I got it, and since I duplicated the bottom section as exactly as I could, I got the same result. Duh! (Don't worry, the baffles weren't secured here. That's why they were cockeyed!)
So my question is: Should I just start over and make a mandrel to fit the hole in the nose bowl and the prop shaft and hang it there to make templates to redo all the cowl sections? I think if I can shift the works up 1/2" or so, I can easily put the REM37BY plugs in without bumps and not even mess with the Ercoupe cups.
Thanks,
Josh Brehm
NC24369
Winterville, NC
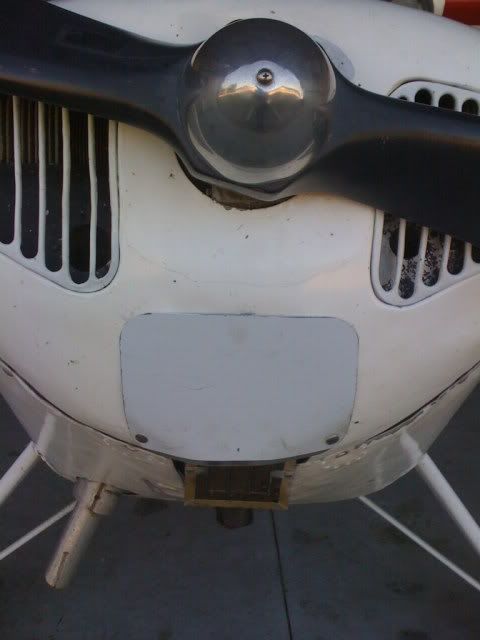
my BL-65 was converted to a Continental back in '65-'65. I've got cowl bumps and cracks in the panels. I've been working hard to rebuild the bottom cowl section and am pretty happy with the results:

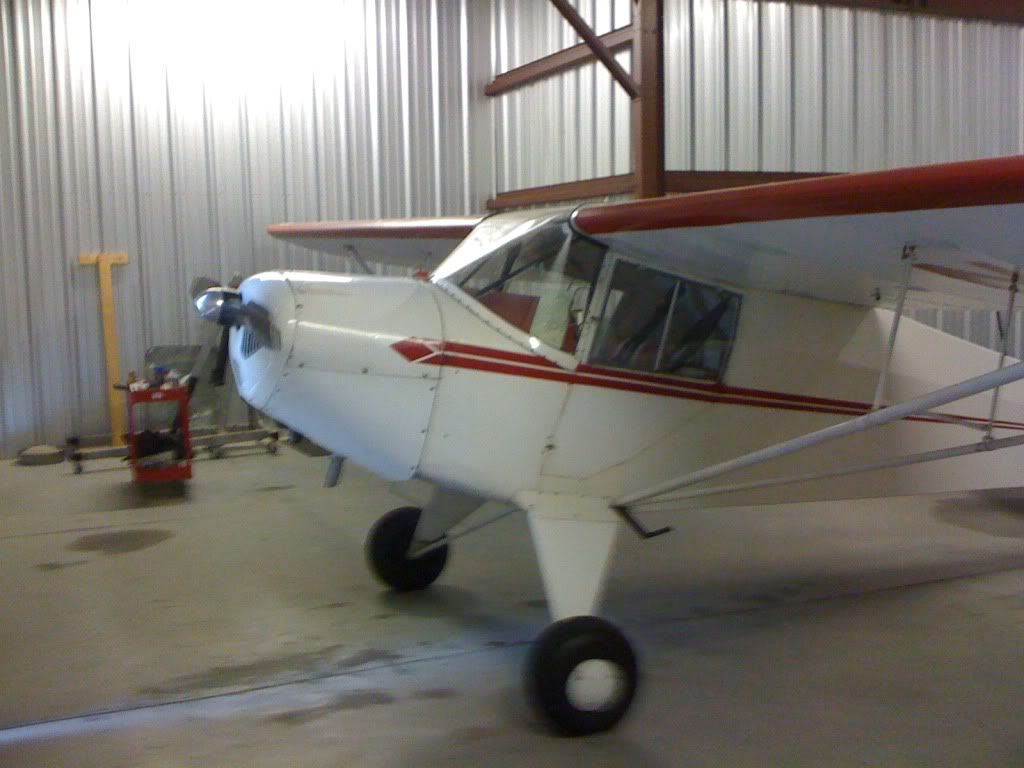
So now I need to tackle the top cowl sections. I'd love to get rid of the cowl bumps, but I have NO clearance on the top. Looking at the nose bowl from the front, I have very little gap at the top and lots at the bottom of the prop hub hole.
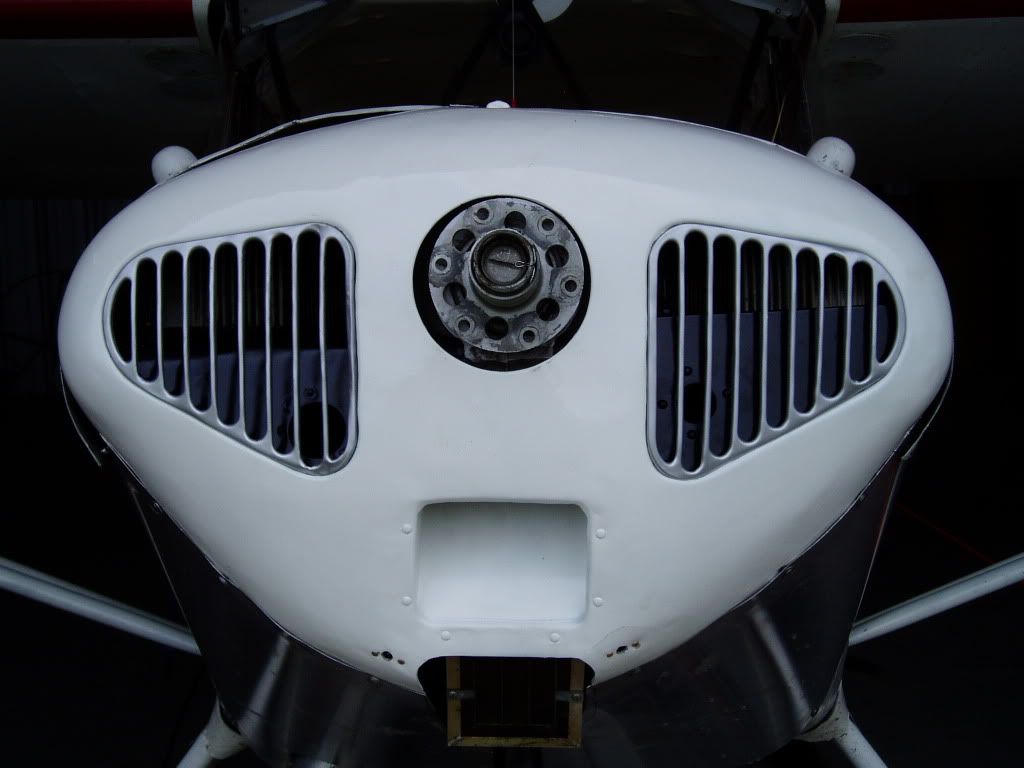
It was like this when I got it, and since I duplicated the bottom section as exactly as I could, I got the same result. Duh! (Don't worry, the baffles weren't secured here. That's why they were cockeyed!)
So my question is: Should I just start over and make a mandrel to fit the hole in the nose bowl and the prop shaft and hang it there to make templates to redo all the cowl sections? I think if I can shift the works up 1/2" or so, I can easily put the REM37BY plugs in without bumps and not even mess with the Ercoupe cups.
Thanks,
Josh Brehm
NC24369
Winterville, NC
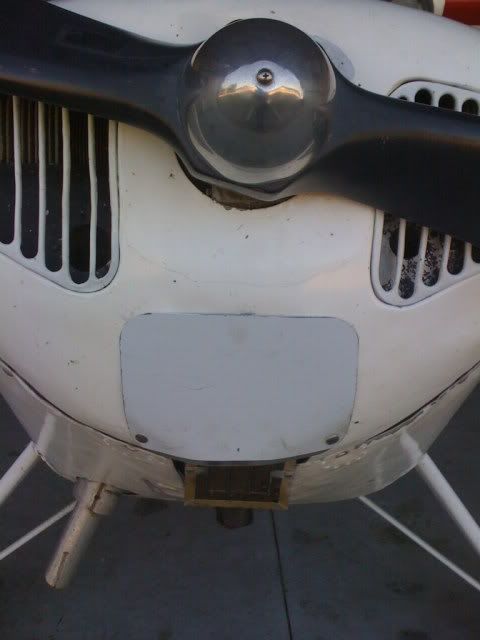
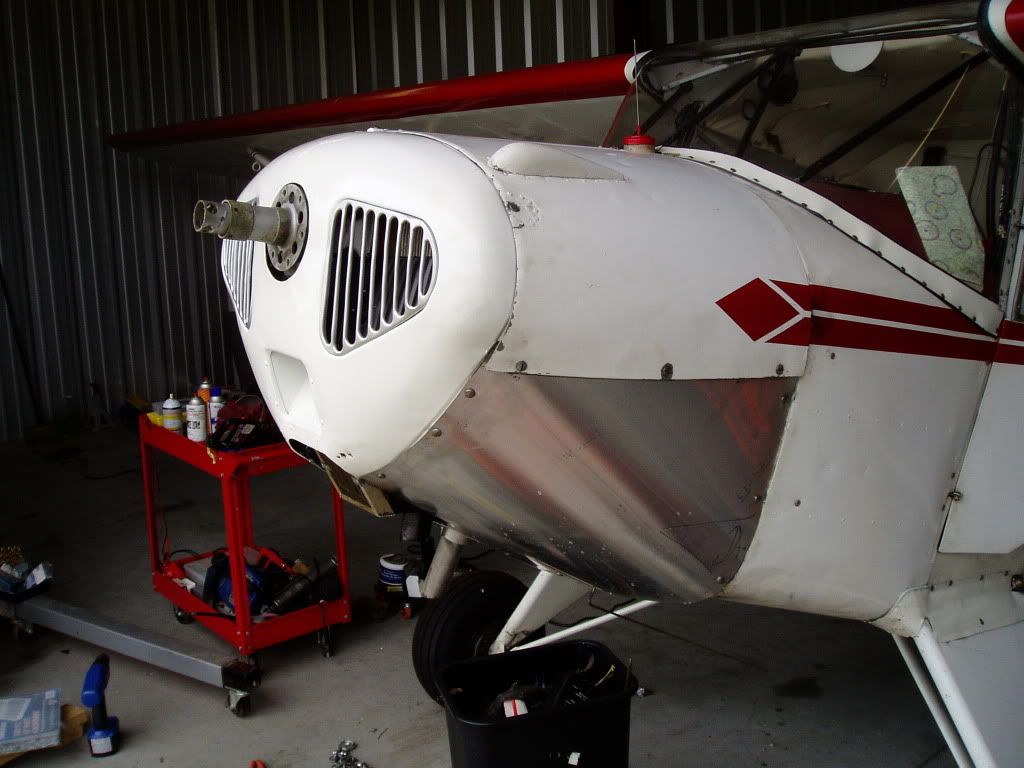
Comment